Sustainability | ~ 3 min read
EV batteries: a second lease of life?
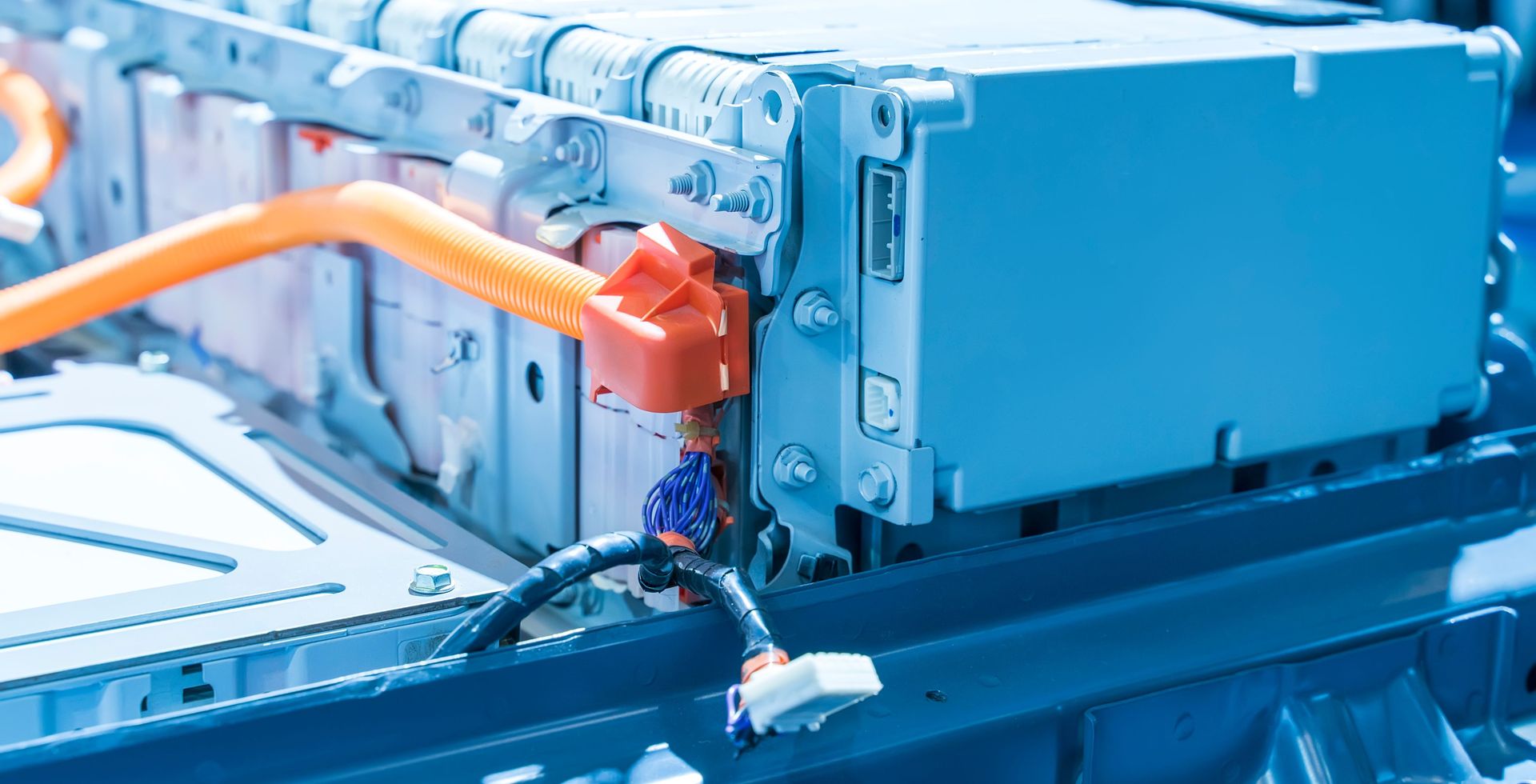
Electric vehicles (EVs) are a critical element in a lower carbon transport system, but sourcing the necessary materials – which include lithium, cobalt and nickel – has a financial and environmental cost. One way to meet the demand for these materials is battery recycling.
It is well known that EV batteries require significant resources to manufacture. Some 660 kilotons of critical materials were used to produce 14 million electric cars sold globally in 2023.1 These numbers are set to grow, as almost 60 million electric cars need to be sold annually by 2030 to meet net zero.2
There is growing pressure to regulate battery recycling globally. Initiatives such as the Inflation Reduction Act in the US and the EU’s New Battery Directive – as well as the introduction of battery recycling liabilities for auto manufacturers in China – are setting standards for recycling. These standards are set to become more stringent over time and are being mirrored in locations such as Japan and South Korea. We think regulation could be a key driver in the uptake of battery recycling.
Not the end of the road for batteries
The mainstreaming of EV battery recycling is a necessity as the number of EV batteries that have reached the end of life is projected to surpass 10 million units in 2035.3 This challenge is an opportunity, since the sheer number of batteries available to be recycled offers potential economies of scale for new facilities and auto manufacturers. There is the possibility to fully integrate recycling into the lifecycle management of vehicles.
A resilient and integrated recycling system also lowers the geopolitical and location risks involved in sourcing materials, while reducing exposure to volatile raw material markets. Early adoption of circular business models can provide an early-mover advantage in an environment of tightening regulation as well as the opportunity to influence industry standards.
Recycling batteries is complex and requires technical and operational expertise. There are health and safety risks associated with mechanical disassembly, pollution risks for chemical treatment, and significant energy and carbon intensity required for pyrometallurgical processes. Recycling nickel manganese cobalt (NMC) batteries is more economically viable than lithium iron phosphate (LFP) batteries; over time, this difference in cost could influence vehicle design decisions.
An engaging topic
AllianzGI has launched a thematic engagement project on EV battery recycling. We have started with auto and battery manufacturers but will extend to relevant upstream and downstream sectors. We aim to understand the economic, regulatory and compliance considerations of a resilient, circular EV battery business model. We also look to secure time-bound strategic and disclosure commitments through the industry’s value chain.
1 Source: International Energy Agency. The total weight of materials is calculated by multiplying the average weight of materials for a car (47 kilos) by the figure of 14 million.
2 Electric car sales and sales share in the Net Zero Scenario, 2015-2030. Projected sales of nearly 60 million a year would account for two-thirds of total sales in 2030.
3 “EV Battery Recycling: Implications of the incoming EU Directive”, Barclays Equity Research, 31 January 2023, p7. The estimate only includes passenger EV batteries. Source: BloombergNEF, Rho Motion, Barclays Research.